- 06
- Oct
Cleaner production process of flexible circuit board
Cleaner production process of esnek devre kartı
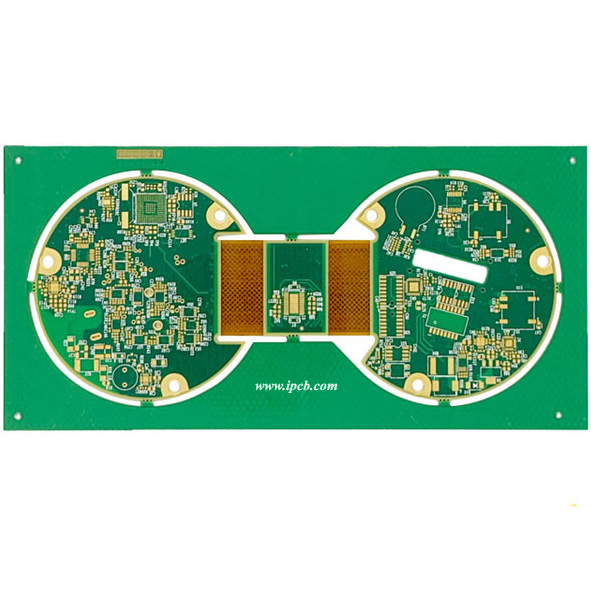
1. Direct metallization (DMS): ethylenediamine tetraacetic acid (EDTA) is contained in the chemical copper precipitation solution as a chelating agent, and most printed circuit board manufacturers do not have the technology to recover ethylenediamine tetraacetic acid, so the use of chemical copper precipitation is limited. At present, the more advanced is the direct metallization method (DMS) without chemical copper deposition. Instead, fine carbon powder is dipped and coated on the hole wall to form a conductive layer. After micro etching, the carbon base on the copper layer is removed, and only the conductive carbon film layer is retained on the non conductor (insulating epoxy resin substrate) inside the hole wall, and then directly electroplated. In simultaneous interpreting, the new fully enclosed equipment was used in electroplating. Compared with the traditional electroplating bath, the emission of waste gas to the outside was reduced by more than 95%, the discharge of sewage was reduced by about 1 / 3, and the concentration of pollutants in the waste liquid was low. At the same time, due to the good sound insulation effect of the equipment and the installation of silencing device of forced draft fan, the noise pollution is greatly reduced.
2. Pure tin electroplating method: using pure tin electroplating instead of tin lead electroplating can eliminate the pollution of heavy metal lead. According to the thickness of lead tin plating layer of circuit board 10 m, the amount of lead in 1t waste liquid is 18 ~ 20 kg. According to the amount of tin stripping waste liquid 52.1t/a, the lead emission can be reduced by 937.8 ~ 104.0kg/a.
3. Add water roller and air knife: water absorption roller and air knife are set between ammonia copper etching section and water washing section, so that the etching solution can be fully utilized in the etching tank, and the amount of ammonia copper brought out by discharged sewage can be reduced by 80% compared with the traditional method, reducing the difficulty and cost of wastewater treatment. In the developing machine section and water washing section, water absorption rollers and air knives are set, so that the developer can be fully utilized in the developing tank and the amount of potassium carbonate brought out by the discharged sewage is greatly reduced. Relevant exhaust locations are provided with exhaust gas outlets, which are directly connected with the exhaust gas pipeline during exhaust, and the exhaust gas enters the treatment facilities to avoid leakage. At the same time, the water from the last washing of the developer is reused in the etching section, saving a lot of fresh water.
4. Fully enclosed equipment: the oxidation section adopts fully enclosed equipment, and the waste gas overflow is more than 95% lower than that of the traditional blackening tank. The front section of the system is equipped with a drying oven. Compared with the blackening line separated from the oven, the organic waste gas can be collected and treated better and reduce its overflow. The equipment has good sound insulation effect, and the silencing device of forced draft fan can greatly reduce the noise pollution.
5. Changing the rack: changing the rack and covering the rack with tin can prolong the frequency of changing the tank of nitric acid solution of the rack from 2D / time to 7d / time, and reduce the sewage discharge.
6. Using nitric acid instead of fluoroboric acid: using nitric acid instead of fluoroboric acid to remove tin can eliminate fluorine pollution.
7. Using CAD and photo plate making: using CAD and photo plate making technology can improve the quality of photographic plate and reduce the waste and pollution of photographic plate.
8. Using laser direct imaging technology: using laser direct imaging technology can save the photographic plate making process, so as to avoid the waste and pollution of photographic negatives.