- 06
- Oct
Quy trình sản xuất bảng mạch linh hoạt sạch hơn
Quy trình sản xuất sạch hơn của bảng mạch linh hoạt
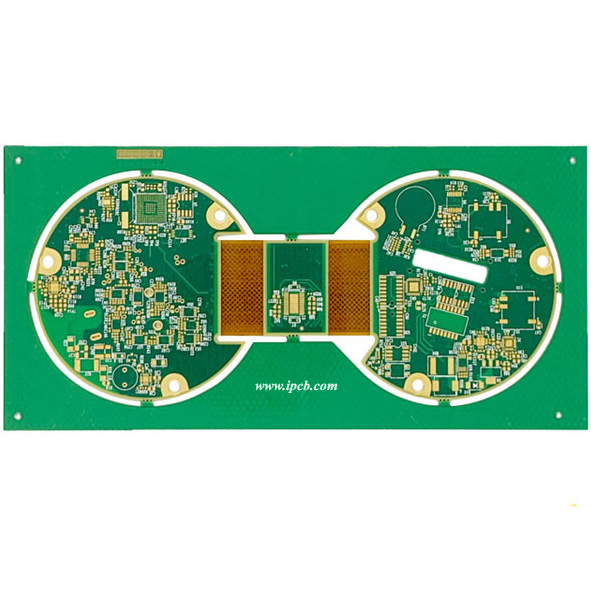
1. Kim loại hóa trực tiếp (DMS): axit tetraacetic etylendiamine (EDTA) được chứa trong dung dịch kết tủa đồng hóa học như một tác nhân tạo chelating, và hầu hết các nhà sản xuất bảng mạch in không có công nghệ thu hồi axit tetraacetic ethylenediamine, vì vậy việc sử dụng đồng hóa học lượng mưa bị hạn chế. Hiện nay, tiên tiến hơn là phương pháp kim loại hóa trực tiếp (DMS) không lắng đọng đồng hóa học. Thay vào đó, bột carbon mịn được nhúng và phủ lên thành lỗ để tạo thành một lớp dẫn điện. Sau khi ăn mòn vi mô, cơ sở carbon trên lớp đồng bị loại bỏ, và chỉ lớp phim carbon dẫn điện được giữ lại trên vật liệu không dẫn điện (nền nhựa epoxy cách điện) bên trong thành lỗ, và sau đó được mạ điện trực tiếp. Trong phiên dịch đồng thời, thiết bị mới hoàn toàn kèm theo đã được sử dụng trong quá trình mạ điện. So với bể mạ điện truyền thống, lượng khí thải ra bên ngoài giảm hơn 95%, lượng nước thải giảm khoảng 1/3 và nồng độ các chất ô nhiễm trong chất lỏng thải thấp. Đồng thời, do thiết bị có tác dụng cách âm tốt và việc lắp đặt thiết bị giảm thanh của quạt hút cưỡng bức nên giảm thiểu ô nhiễm tiếng ồn.
2. Phương pháp mạ điện thiếc tinh khiết: sử dụng phương pháp mạ điện thiếc tinh khiết thay cho phương pháp mạ điện chì thiếc có thể loại bỏ sự ô nhiễm của chì kim loại nặng. Theo độ dày của lớp mạ thiếc chì trên bảng mạch 10 m, lượng chì trong 1t chất lỏng thải là 18 ~ 20 kg. Theo lượng chất lỏng thải thiếc 52.1t / a, lượng chì phát thải có thể giảm 937.8 ~ 104.0kg / a.
3. Thêm con lăn nước và dao không khí: con lăn hấp thụ nước và dao không khí được đặt giữa phần ăn mòn đồng amoniac và phần rửa nước, để dung dịch ăn mòn có thể được sử dụng đầy đủ trong bể ăn mòn và lượng đồng amoniac được đưa ra ngoài bằng lượng nước thải thải ra có thể giảm 80% so với phương pháp truyền thống, giảm khó khăn và chi phí xử lý nước thải. Trong phần máy đang phát triển và phần rửa nước, con lăn hấp thụ nước và dao không khí được thiết lập, để nhà phát triển có thể sử dụng đầy đủ trong bể đang phát triển và lượng kali cacbonat mang theo nước thải thải ra ngoài được giảm đáng kể. Các vị trí xả thải có liên quan được bố trí các cửa thoát khí thải, được kết nối trực tiếp với đường ống dẫn khí thải trong quá trình xả, khí thải đi vào các công trình xử lý để tránh rò rỉ. Đồng thời, nước từ lần giặt cuối cùng của nhà phát triển được tái sử dụng trong phần khắc, tiết kiệm rất nhiều nước ngọt.
4. Thiết bị kín hoàn toàn: phần oxy hóa sử dụng thiết bị hoàn toàn kín, và lượng khí thải tràn xuống thấp hơn 95% so với bể hóa đen truyền thống. Phần phía trước của hệ thống được trang bị một tủ sấy. So với dây chuyền hóa đen tách ra khỏi lò, khí thải hữu cơ có thể được thu gom và xử lý tốt hơn và giảm tình trạng tràn ra ngoài. Thiết bị có tác dụng cách âm tốt, thiết bị giảm thanh của quạt hút cưỡng bức có thể giảm thiểu ô nhiễm tiếng ồn.
5. Thay giá: thay giá và phủ thiếc vào giá có thể kéo dài tần suất thay thùng chứa dung dịch axit nitric của giá từ 2D / lần lên 7ng / lần, đồng thời giảm lượng nước thải.
6. Sử dụng axit nitric thay vì axit flohidric: sử dụng axit nitric thay cho axit flohidric để khử thiếc có thể loại bỏ ô nhiễm flo.
7. Sử dụng CAD và chế tạo tấm ảnh: sử dụng CAD và công nghệ tạo tấm ảnh có thể cải thiện chất lượng tấm ảnh và giảm chất thải và ô nhiễm của tấm ảnh.
8. Sử dụng công nghệ chụp ảnh trực tiếp bằng laser: sử dụng công nghệ chụp ảnh trực tiếp bằng laser có thể tiết kiệm quá trình tạo tấm ảnh, để tránh lãng phí và ô nhiễm của âm bản ảnh.